Table of Contents
Understanding ABC Analysis
ABC analysis is an inventory categorization technique that divides items into three categories based on their importance:
- Category A: These are the most valuable items, representing a small percentage of the total inventory, but accounting for a significant portion of the overall value. Typically, Category A items comprise about 20% of the inventory but contribute 70-80% of the inventory value.
- Category B: These items are of moderate value, making up a larger portion of the inventory than Category A items, but contributing less to the total value. Category B items usually constitute about 30% of the inventory and account for 15-25% of the inventory value.
- Category C: These are the least valuable items, representing a large portion of the inventory but contributing the least to the overall value. Category C items often make up about 50% of the inventory, but only 5-10% of the inventory value.
The primary objective of ABC analysis is to focus resources and management efforts on the most critical items (Category A), while still maintaining control over less critical items (Categories B and C). This approach allows businesses to allocate their resources more efficiently and effectively.
Applying ABC Analysis to Warehousing
ABC analysis can be applied to various aspects of warehousing to optimize operations and enhance efficiency. Here are some key areas where ABC analysis can be beneficial:
Inventory Management
In warehousing, managing inventory effectively is crucial for meeting customer demands and minimizing costs. ABC analysis helps prioritize inventory management efforts based on the value and importance of items. By focusing on Category A items, businesses can ensure that these high-value products are always available and well-managed. This approach reduces the risk of stockouts and overstock situations, leading to improved customer satisfaction and reduced carrying costs.
Space Optimization
Efficient use of warehouse space is vital for maximizing storage capacity and reducing operational costs. ABC analysis can help optimize space utilization by allocating prime storage locations to Category A items, which are the most frequently accessed and valuable. Category B items can be stored in less accessible locations, while Category C items can be placed in the least accessible areas.
This strategic placement reduces picking times and increases overall warehouse efficiency.
Cost Reduction
By focusing on high-value items, ABC analysis helps businesses identify and eliminate inefficiencies in their inventory management processes. For instance, businesses can implement just-in-time (JIT) inventory strategies for Category A items to reduce carrying costs and minimize the risk of obsolescence. Additionally, ABC analysis can help identify slow-moving or obsolete items in Categories B and C, allowing businesses to implement targeted strategies for reducing excess inventory and associated costs.
Improved Supplier Relationships
Managing supplier relationships effectively is essential for ensuring a reliable supply of inventory and minimizing lead times. ABC analysis enables businesses to prioritize their relationships with suppliers based on the value and importance of items. By focusing on Category A items, businesses can negotiate better terms, secure favorable pricing, and establish stronger partnerships with key suppliers. This approach ensures a steady supply of high-value items and reduces the risk of disruptions in the supply chain.
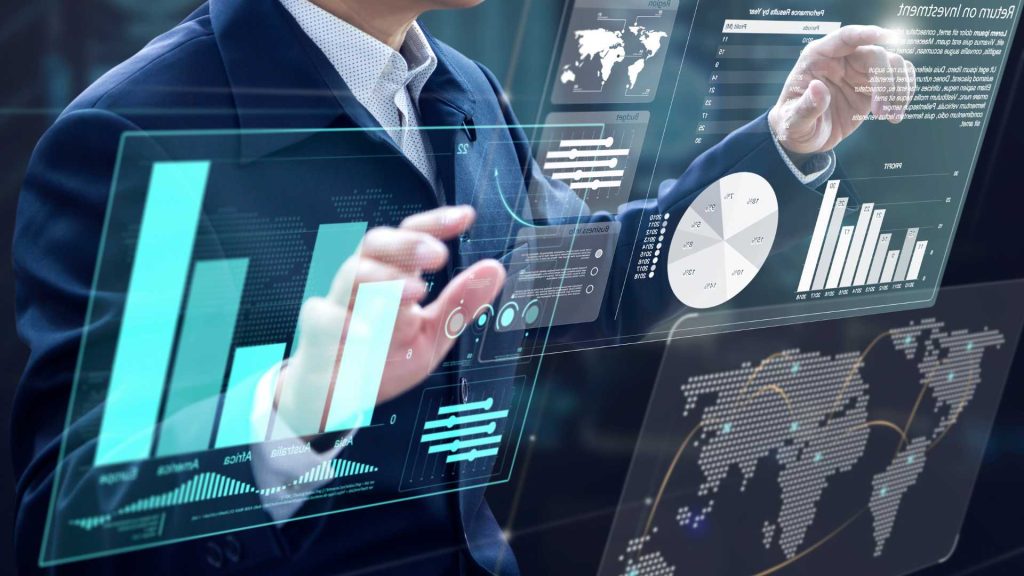
Enhanced Inventory Control
ABC analysis provides a structured approach to inventory control by segmenting items based on their importance. Implement strict control measures such as regular cycle counts, detailed tracking, and frequent reviews for Category A items to ensure accuracy and availability.
Category B and C items, while less critical, still require periodic reviews to maintain optimal stock levels. This enhanced control reduces discrepancies, improves inventory accuracy, and ensures that resources are focused where they are most needed.
Strategic Purchasing Decisions
ABC analysis informs strategic purchasing decisions by highlighting which items require more attention and resources. With Category A items, businesses can establish long-term contracts with reliable suppliers to ensure consistent quality and supply. For Category B items, purchasing decisions can focus on balancing cost and demand, while Category C items may be sourced in bulk to reduce costs. This strategic approach to purchasing helps in maintaining optimal inventory levels, reducing costs, and ensuring a reliable supply chain.
Implementing ABC Analysis in Warehousing
Implementing ABC analysis in your warehouse involves several steps. Here is a step-by-step guide to help you get started:
1: Data Collection
The first step in implementing ABC analysis is to collect data on your inventory items. This data should include information such as item descriptions, quantities, and the total value of each item. Additionally, gather data on sales volumes, demand patterns, and lead times for each item.
2: Categorization
Once you have collected the necessary data, categorize your inventory items into Categories A, B, and C based on their value and importance. Use the 80/20 rule as a guideline: Category A items should represent approximately 20% of the inventory but account for 70-80% of the total value. Category B items should constitute about 30% of the inventory and contribute 15-25% of the value, and Category C items should make up about 50% of the inventory and account for 5-10% of the value.
3: Analysis and Segementation
Analyze your inventory data to identify patterns and trends. Segment your inventory into the three categories and calculate the percentage of items and value each category represents. This analysis will help you understand the distribution of value across your inventory and identify areas for improvement.
4: Strategy Development
Develop targeted strategies for managing each category of inventory. For Category A items, implement strict inventory control measures, such as regular cycle counts and just-in-time inventory strategies, to ensure availability and minimize carrying costs. For Category B items, focus on optimizing inventory levels and reducing lead times. For Category C items, consider implementing cost-effective storage solutions and periodic reviews to identify slow-moving or obsolete items.
5: Implementation
Implement the strategies you have developed for each category. This may involve reorganizing your warehouse layout, renegotiating supplier contracts, and implementing new inventory management processes. Ensure that your warehouse staff is trained on the new procedures and understands the importance of ABC analysis in optimizing inventory management.
6: Monitoring and Adjustment
Continuously monitor your inventory performance and adjust your strategies as needed. Regularly review your ABC analysis to ensure that your inventory categorization remains accurate and up-to-date. Adjust your inventory management strategies based on changes in demand patterns, supplier performance, and other factors that may impact your inventory.
7: Integration with Warehouse Management Systems
Integrating ABC analysis with your Warehouse Management System (WMS) can streamline and automate the categorization process, ensuring real-time updates and accurate tracking. Shipedge’s WMS is specifically designed to support ABC analysis, providing robust tools for data collection, categorization, and analysis. By leveraging Shipedge’s WMS, you can automate the implementation of ABC strategies, enhance inventory control, and improve overall operational efficiency.
Conclusion
ABC analysis is a powerful tool for optimizing inventory management in warehousing. By categorizing inventory items based on their value and importance, businesses can allocate resources more efficiently, optimize space utilization, reduce costs, and improve supplier relationships.
Implementing ABC strategies involves collecting data, categorizing inventory items, analyzing and segmenting data, developing targeted strategies, integrating with a robust WMS like Shipedge, and continuously monitoring and adjusting your approach. By following these steps, businesses can enhance their inventory management processes and achieve greater operational efficiency in their warehousing operations.
Incorporating this into your warehousing strategy can lead to significant improvements in efficiency, cost savings, and overall business performance. Whether you are managing a small warehouse or a large distribution center, ABC strategies help provide a structured approach to inventory management that can help you meet customer demands, reduce costs, and improve your bottom line.