In an era characterized by rapid technological advancements and shifting consumer demands, the warehousing sector is not immune to the pressing need for evolution. One key to sustained success is fostering a culture of continuous improvement. Cultivating such a culture can increase efficiency, reduce costs, and enhance employee morale. Here’s how to create a culture of continuous improvement in warehousing.
Table of Contents
- 1. Invest in Training and Development
- 2. Celebrate Small Wins
- 3. Implement Key Performance Indicators (KPIs)
- 4. Embrace a Problem-solving Mindset
- 5. Leverage Technology and Automation
- 6. Encourage Cross-training
- 7. Foster a Rewarding Environment
- 8. Regularly Review and Refine Processes
- 9. Stay Updated with Industry Best Practices
- Maintain Improvement in Warehousing
1. Invest in Training and Development
The warehousing industry, like many other sectors, is undergoing rapid transformation due to technological advancements and evolving best practices. With these changes come new tools, techniques, and strategies. To remain competitive and drive continuous improvement, it is vital to prioritize the ongoing education and training of your team.
- Customized Training Programs: Design training programs tailored to the unique requirements and challenges of your warehouse operations. This could range from hands-on sessions with new equipment to classroom-based learning on inventory management theories.
- External Workshops and Seminars: Encourage team members to attend industry-specific workshops and seminars. Exposure to external experts and different viewpoints can introduce fresh perspectives and innovative solutions.
- Continuous Learning Platforms: Invest in online platforms or subscription services that offer courses on emerging warehousing technologies, methodologies, and strategies. This ensures that your team can learn at their own pace and stay updated.
2. Celebrate Small Wins
In the pursuit of major milestones and significant achievements, the smaller, incremental improvements often get overlooked. Yet, it’s these small wins that collectively contribute to large-scale success.
- Regular Recognition: Create a platform or a system where team members can regularly highlight and share their achievements, however minor they might seem. This could be a weekly team meeting or a dedicated bulletin board.
- Rewarding Efforts: Tangible rewards, be it small bonuses, gift cards, or even an ‘Employee of the Month’ feature, can significantly boost morale. When employees feel their efforts are acknowledged, they’re more likely to be proactive in their roles.
- Foster a Positive Environment: Celebrating small victories contributes to a positive work environment. It shifts the focus from what’s lacking or mistakes made, to progress and growth.

3. Implement Key Performance Indicators (KPIs)
In the realm of warehousing, there are myriad metrics that can be monitored. However, not all metrics align with the goals of continuous improvement. KPIs need to be carefully selected to ensure they’re driving the desired change.
- Align with Objectives: KPIs should be in line with the broader objectives of the warehouse. For instance, if the goal is to reduce order processing time, then a relevant KPI might be ‘Average Time to Fulfill an Order’.
- Data-driven Decisions: Regularly monitoring and analyzing KPI data can highlight trends, uncover inefficiencies, and provide insights into areas that require attention. This data-centric approach removes guesswork and paves the way for informed decisions.
- Flexibility in KPIs: The warehousing industry is dynamic. As such, the KPIs set at the beginning of the year might not remain relevant throughout. Periodically review and adjust your KPIs to ensure they reflect current objectives and challenges.
By expanding your focus on training, celebrating every step of progress, and implementing relevant KPIs, you’ll be well on your way to embedding a culture of continuous improvement within your warehousing operations.
4. Embrace a Problem-solving Mindset
Addressing challenges proactively, instead of reacting to them, can greatly enhance warehouse efficiency and productivity. Adopting a problem-solving mindset involves a two-fold approach: identifying issues at their nascent stages and fostering an environment where every team member feels empowered to voice concerns and suggest solutions.
- Root Cause Analysis: Implement tools and strategies like the “5 Whys” technique to trace back to the root cause of any problem. Instead of just dealing with the symptoms, get to the core of the issue.
- Open Communication Channels: Set up platforms or regular meetings where employees at all levels can share their observations and insights. Front-line workers often spot potential challenges before they escalate.
- Continuous Feedback Loop: Ensure that when problems are identified and solutions implemented, the outcomes are communicated back to the team. This not only reinforces the importance of a problem-solving approach but also fosters a sense of collective ownership and collaboration.
5. Leverage Technology and Automation
In today’s rapidly evolving warehousing landscape, technology and automation aren’t just enhancements; they’re necessities. Embracing these can drastically transform operations, reduce human errors, and boost overall efficiency.
- Warehouse Management Systems (WMS): Implement advanced WMS that integrates seamlessly with other business software. It can optimize inventory levels, streamline picking processes, and provide real-time data analytics, laying the groundwork for more informed decision-making.
- Automated Picking Routes: The likelihood that your warehouse pickers can identify the best picking route every time they retrieve orders in the warehouse is slim to none. Using a WMS that identifies the best route possible for you helps reduce travel time and errors.
- Data Analytics: Use advanced analytics to forecast demand, optimize inventory, and predict trends. Algorithms can offer insights that humans might overlook, leading to further refinements in operations.
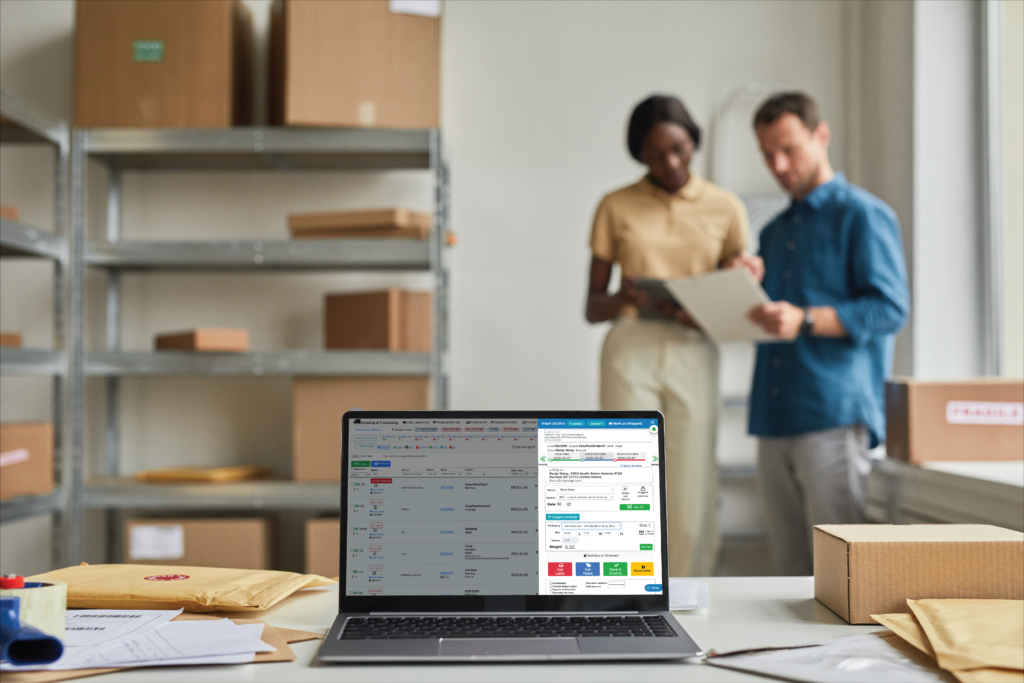
6. Encourage Cross-training
Cross-training not only provides a backup during employee absences but also instills a holistic understanding of the warehousing operations amongst the staff.
- Versatile Workforce: With cross-training, employees can easily switch roles as needed, ensuring that the workflow isn’t hampered during peak times or during staff shortages.
- Improved Collaboration: When team members understand the challenges and responsibilities of their colleagues in different roles, they can collaborate more efficiently, ensuring smoother operations.
- Skill Enhancement: Cross-training provides employees with an opportunity to learn new skills and understand various facets of warehousing. This not only boosts their morale and job satisfaction but also prepares them for potential leadership roles in the future.
While all these strategies are vital, the linchpin is the integration of technology and automation in warehousing. As the sector pivots towards these advancements, businesses that harness their full potential will undoubtedly lead the pack in efficiency, productivity, and customer satisfaction.
7. Foster a Rewarding Environment
Creating a rewarding environment goes beyond monetary incentives. It’s about recognizing hard work, innovation, and commitment, and ensuring that employees are engaged and invested in the warehouse’s continuous improvement journey.
- Employee Recognition Programs: Regularly spotlight employees who’ve made significant contributions or showcased exceptional problem-solving skills. This can be done through ‘Employee of the Month’ awards or showcasing their achievements in internal communications.
- Feedback-driven Improvements: When employees suggest an operational change or process improvement that’s implemented, acknowledge their contribution. This not only motivates them but also encourages others to come forward with their insights.
- Skill Development: Invest in workshops, training sessions, and courses that can help employees upskill. This not only enhances their professional growth but also benefits the warehouse with improved skills and expertise.
8. Regularly Review and Refine Processes
As the business landscape and customer demands evolve, so should warehouse operations. Regular reviews ensure that processes remain relevant, efficient, and aligned with the organization’s objectives.
- Quarterly Audits: Conduct comprehensive audits to identify bottlenecks, redundant processes, or areas needing improvement. This helps in keeping the operations streamlined.
- Feedback Collection: Use tools or regular meetings to collect feedback from both staff and clients. This provides a dual perspective – internal operational challenges and external customer satisfaction metrics.
- Scalability Consideration: As the business grows, the warehousing needs will change. Ensure that processes are scalable and adaptable to accommodate future growth without major overhauls.
9. Stay Updated with Industry Best Practices
The improvement in warehousing science is continuous. Staying abreast of the latest trends and best practices can provide insights into potential areas of improvement for any warehouse.
- Industry Conferences and Workshops: Attend relevant conferences, seminars, or workshops. These platforms provide insights into emerging trends, tools, and strategies being adopted worldwide.
- Trade Publications: Subscribe to industry-specific magazines, journals, and online publications. These resources often feature case studies, expert opinions, and articles on the latest advancements.
- Networking: Engage with industry peers, competitors, and experts. Exchanging experiences and challenges can lead to fresh perspectives and innovative solutions.
Maintain Improvement in Warehousing
In the dynamic world of warehousing, the path to excellence is paved with consistent effort, adaptability, and a relentless pursuit of improvement. While technology plays an important role, the human element – fostering a culture of continuous growth, valuing feedback, and investing in employee development – remains paramount. As businesses and the ecosystem evolve, warehouses that prioritize both technology and their people will find themselves well-equipped to navigate future challenges and capitalize on emerging opportunities.