In the fast-paced, challenging world of eCommerce, the efficiency of your warehouse operations can make or break your business. A critical component of these operations is picking and packing. But what exactly is picking and packing? And how can you ensure these processes are as efficient as possible? The answer to these questions lies in the power of advanced technology solutions, like those offered by Shipedge.
Table of Contents
What is Picking and Packing?
Picking and packing are the two essential steps in the order fulfillment process. \
Picking refers to the process of selecting, or “picking,” the appropriate items from your warehouse inventory to fulfill an order. Once the correct items are picked, they then move to the packing stage.
Packing involves securely wrapping or boxing these items to prepare them for shipment.
Given their crucial role in order fulfillment, it’s imperative that your picking and packing processes are efficient and accurate. Inaccuracies or inefficiencies can lead to order mistakes, increased returns, and dissatisfied customers. Consequently, ensuring efficient picking and packing is critical to successful eCommerce operations.
Picking and Packing in eCommerce
Picking and packing might seem like straightforward processes, but their influence on your eCommerce business’s success should not be underestimated. Incorrect picking can lead to wrong items being sent out, resulting in returns, refunds, and dissatisfied customers.
Similarly, improper packing for shipping can result in damaged goods, which again leads to customer dissatisfaction and potential losses for your business. Therefore, optimizing your pick and pack operations is a must for achieving eCommerce success.
How to Pick and Pack: Best Practices
- Accuracy is key: Make sure the correct items are picked for each order. Any mistake in this step can result in incorrect order fulfillment and subsequent returns.
- Organize your warehouse: Having a well-organized warehouse can significantly speed up the picking process. This can be achieved by logically grouping items and clearly marking aisles and bins.
- Use the right packaging materials: Depending on the nature of the items, choose appropriate packaging materials to ensure their safety during transit.
- Consider the order size: Use a box that is just the right size for the order. An excessively large box can increase shipping costs and the risk of damage. Utilizing tools like cartonization engines can help make this process quicker and more accurate
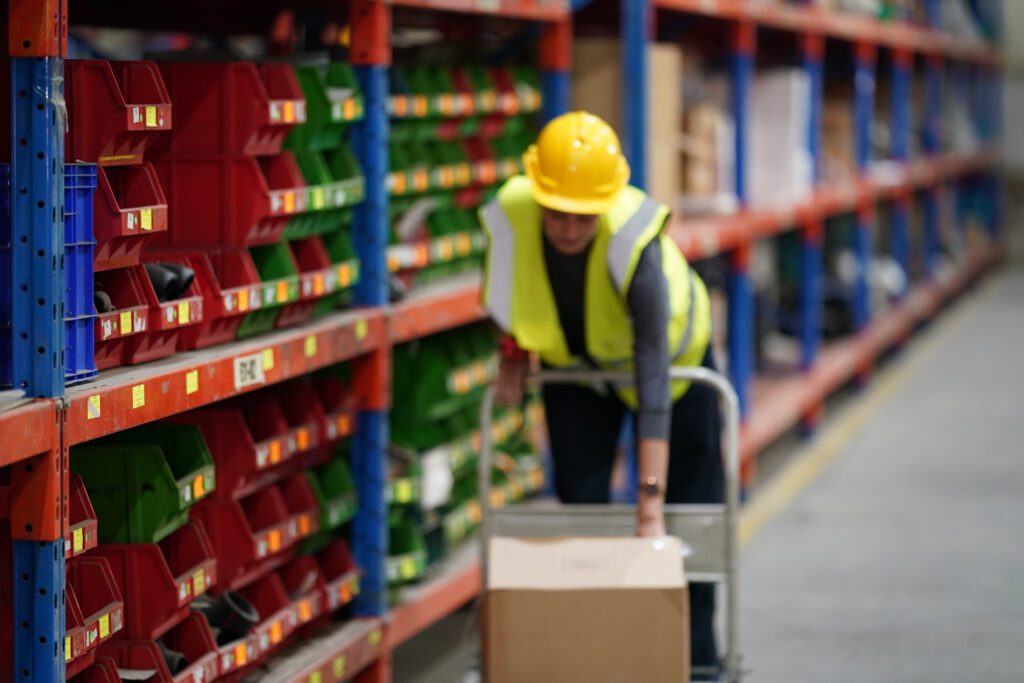
Different Picking Methods
The most optimal picking method varies from warehouse to warehouse. There are many factors that go into determining the best routes for your laborers to pick orders. What does your warehouse layout look like? Where do you keep high-volume orders? Do you usually pick multiple items for one order? These are all questions to ask yourself to help determine the best picking method.
Listed below are just a few of the many different types of picking methods.
Batch Picking
An extremely common type of picking, especially in the eCommerce sector, batch picking entails grouping orders into small batches. An employee will then pick all orders within the batch in one pass. For businesses that handle many small orders concurrently, batch picking can increase efficiency by reducing the time spent going back and forth in the warehouse. This method works best when orders have at least one product in common, allowing the picker to pick quantities of the same item at once before moving on to the next item.
Serpentine Picking
Perhaps one of the more visually pleasing styles of picking, serpentine picking follows a path that weaves between the rows of your warehouse. Serpentine picking is commonly used when dealing with high-volume fulfillment centers requiring a lot of picks in a short period of time.
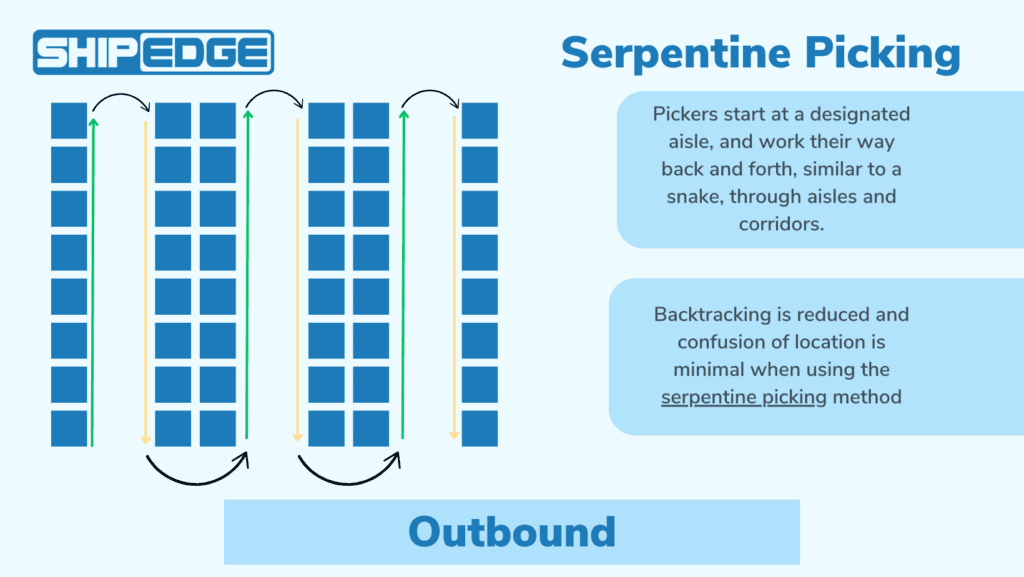
Cluster Picking
Similar to batch picking, cluster picking involves grouping orders together. However, the key difference is that in cluster picking, each order in the batch is assigned to a separate bin or tote. As the picker moves through the warehouse, they pick items for all orders in the batch at once, placing each item into its corresponding bin. This method is particularly useful when orders consist of a small number of different items, as it allows for multiple orders to be picked simultaneously, reducing travel time.
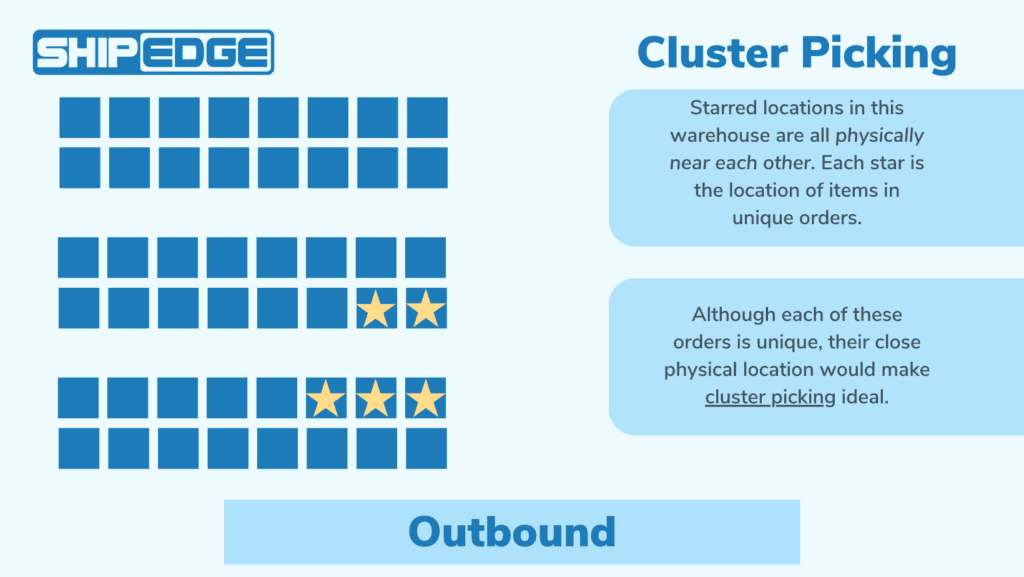
Zone Picking
As part of Shipedge’s years of warehouse science research, we’ve determined the best way to organize your warehouse is in zones. When sectioning your warehouse into separate zones, you allow for greater operational efficiency and visibility into your warehouse. With zone picking, warehouse employees are assigned a specific zone that they will pick orders from.
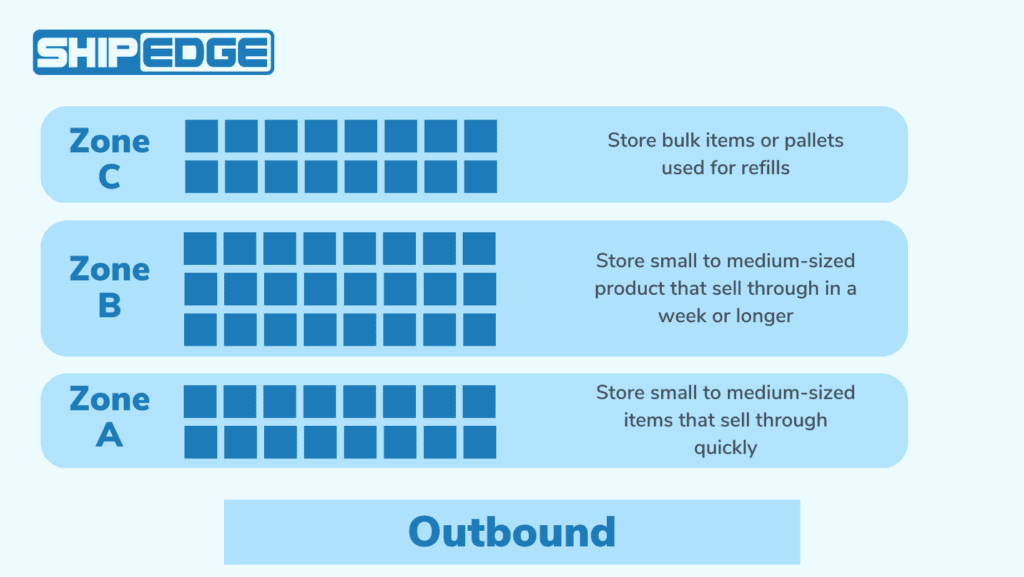
Other Picking Methods
There are more picking methods than those listed above. For more detailed information on the best picking methods for your operations, refer to our guide on 7 effective picking methods.
Optimize Packing Orders
The picking and packing process doesn’t stop when the order has been handed off to packers, there are still more ways to increase operational efficiency in the warehouse at the packing station.
- Reduce packaging waste: Cartonization is a tool that tells your packers what box is best to put a complete order in based on its dimensions. This means that packers don’t need to try multiple boxes before finding the right one or selecting a parcel that’s too large and wastes resources on filler and shipping costs.
- Kitting: One way you can further reduce operational costs is by offering kits, or bundles, of products. Offering a kit can help you move product out of the warehouse faster, storing them together makes it easier for pickers, and packers need fewer resources to package those items together.
Boosting Labor Efficiency with a Warehouse Management SystemLabor management can quickly become a tedious task for warehouse managers, especially when it comes to overseeing picking and packing.Warehouse managers can track important labor-management KPIs such as picks per hour and order accuracy with Shipedge’s built-in labor management system.READ MORE: 9 Essential Warehouse KPIs to Measure PerformanceAfter Picking and Packing: Shipping StrategiesAfter the picking and packing of orders have been completed, it’s time to ship them off to your waiting customers.Shipedge offers best rate shipping, or best rate possible (BRP), after specifying when the order should arrive and its delivery location. This means no more manual searches for the best shipping rates given the weight, location, delivery time, etc. Shipedge’s WMS does this for you. Simply choose your preferred carriers and let the software do the work for you.Additionally, Shipedge offers highly competitive USPS shipping rates. Contact one of our solutions engineers to learn more about how your business can take advantage of these cheap rates.
Conclusion
Picking and packing are more than just steps in the order fulfillment process; they are the heart of your operations. By leveraging advanced technology solutions like Shipedge, you can ensure these processes are accurate, efficient, and cost-effective. Improved picking and packing efficiency not only enhances your operational performance but also boosts customer satisfaction, paving the way for business growth and success.