In this article, we will be exploring the warehouse management system or WMS benefits for your inventory management and order fulfillment operations.
What is a WMS?
A Warehouse Management System (WMS) a software solution that helps to manage your inventory and all aspects of daily stock management or fulfillment operations at a warehouse.
Whether you are a small organization or a global brand, a robust eCommrece warehouse management system can help your company modernize its operations and drive positive customer experiences.
Let’s go over some important features a WMS can, and should, have.
Table of Contents
1. Real-time inventory visibility
Real-time inventory visibility and cross-channel stock availability reporting for eCommerce are core competencies of a good warehouse management system. An organized warehouse for storing inventory and managing order fulfillment also serves as an excellent way to drive efficiency across your entire eCommerce lifecycle.
Some of the biggest benefits of inventory visibility inside the warehouse are the ability to empower your teams to get more done, complete tasks faster, and eliminate the overall amount of repetitive or tedious tasks related to inventory management.
Outside the warehouse, inventory visibility will be sent to all your shopping carts and marketplaces to prevent backorders and ensure positive customer experiences. It’s never fun for your customer service team to let clients know that the products they were so excited to order won’t actually be showing up due to a stock-out event.
Reducing Manual Work
Managing your inventory levels based on hand-filled spreadsheets and manual processes is often an inefficient and challenging task.
Your business might end up walking a fine line between not having the right about of stock that is available for order fulfillment or an exaggerated proportion of capital in inactive inventory if you are reliant on manual channel updates.
The more selling channels you have, the tougher manually updating stock availability becomes. At some point, updating multiple channels manually becomes unmanageable.
An eCommerce warehouse management system will allow you to:
- Receive against purchase orders digitally and utilize a mobile scanner to check inventory inside your warehouse quickly and efficiently
- Store and move inventory around your warehouse without stock getting lost with point-to-point moves by scanning
- Recount stock as orders move into a pick phase and update total available vs physical stock on hand
Avoiding Overselling & Poor Customer Experiences
Great warehouse management systems provide your business with accurate real-time inventory stock levels and help you manage those products in a more organized way.
If you are syncing inventory availability back to online channels or reporting it back to sales teams, you may get yourself into trouble by overselling stock you do not actually have on hand. This can hurt your relationships with your customers and create poor brand experiences.
Your customers will appreciate the ability to trust your stock levels that are reported back to selling channels.

2. Improving Labor Management
A good WMS will have a built-in labor management solution, which helps manage your warehouse team members and the work that they do within your warehouse.
Reducing Labor Costs
There is no doubt that the number of pickers and packers you have, as well as general warehouse staff, can amount to a large proportion of the total cost of warehousing operations and overhead. The costs of hiring, training, and retaining employees have been steadily increasing recently, and in some labor markets are in short supply.
If you’re looking to reduce labor costs, an efficient WMS makes it easy to visualize where inefficiencies lie and give you tools to automate or streamline processes. This makes it easier for businesses to make more educated decisions on how to ensure the productivity and morale of the staff.
Driving Productivity
Labor management tracking and other WMS benefits will help your team to work with greater efficiency, which will be tracked via reporting system and real-time productivity dashboards.
This level of reporting gives you actionable insights to drive productivity inside your warehouse as well as easy-to-use tools to help your team get more done.
We’ve seen many fulfillment centers share individual or group metrics on a dashboard in the warehouse to increase productivity. You can drive competition and even reward your team based on outstanding performances.
Another way to use a WMS to drive productivity is by giving your team the tools they need, like a WMS mobile app, to manage the receiving, picking, packing, cycle counting, and quality control. This will reduce in-warehouse travel time, drive picks per hour, boost morale, and eliminate costly errors.
Having more advanced tools allows your team to do more.
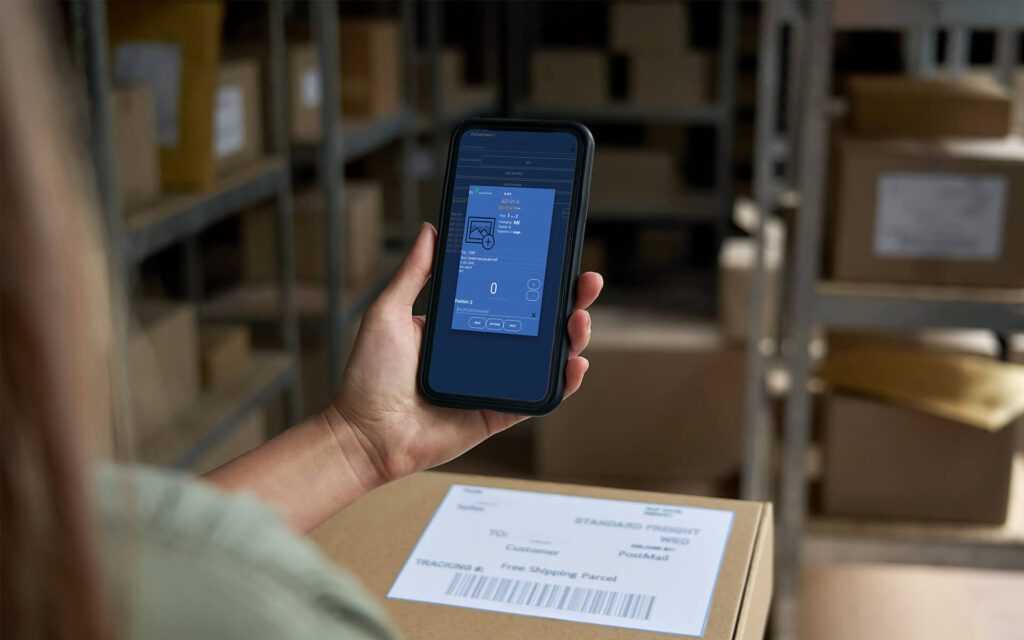
3. Mapping Your Warehouse
How much more efficient would your operations be if your warehouse team could quickly find any product in your warehouse?
What if inventory counts during daily warehouse workflows were more accurate, like receiving, recounts, movement, or picking, by utilizing software tools to prevent errors and verify by scanning?
Would streamlining processes make your warehouse team’s day smoother, and what impact would it have on your team’s morale or overall productivity?
Just like many of you, we’ve asked ourselves these same questions. We’ve come up with advanced warehouse management software tools using our experience in eCommerce inventory and order fulfillment, over the last decade. We are confident that you can utilize our platform so you don’t have to hunt down the answers or solutions all by yourself.
Organizations with world-class fulfillment or distribution programs rely on organized methods of sorting products and robust tools to drive work within the facility.
Creating a well-designed layout of your warehouse site can have the following benefits:
- Better organization and full chain of custody of products in the warehouse
- Increase resource efficiency and decrease labor overhead in the warehouse
- Optimize storage capacity through chaotic storage or other space-saving methods
Warehouse Mapping
A well-designed naming structure should be easy to read to reduce human error. A good way to map your warehouse is based on a structure similar to zone/area, row, bay, and level.
When the time comes to pick an item off the shelf or pallet, it will be easier for your picker to reference where it is. Best-of-breed warehouse management software can turn the tricky process of creating and managing your warehouse mapping process into a breeze!
Check out Shipedge’s warehouse mapping practices 👇
Maximizing Space Utilization
You can also utilize a combination of locations representing a pallet space or shelf location, then pull additional space savings by storing sub-locations or bins of products in that location. Bins can represent a physical case of products or some other more granular storage medium. Typically, a bin can either be fixed-width with a stationary tag, or a flexible-sized case of items tagged with a movable label.
Barcoding Storage Locations
Many warehouse management systems will let you create labels for locations within the application itself. These should be printable, as this lets you quickly and efficiently barcode storage locations within your location.
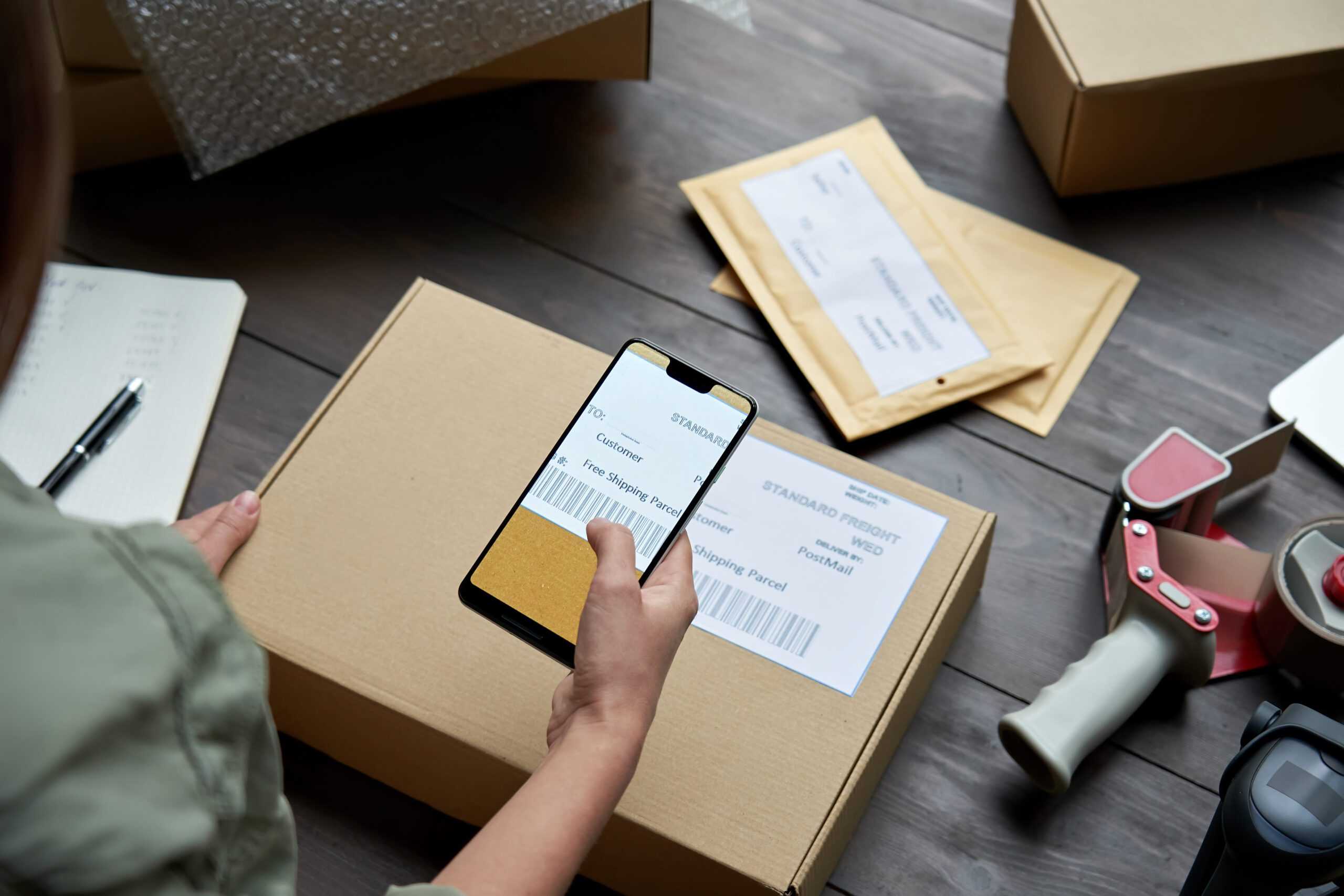
Utilize barcoded location and bin tags to facilitate scan-based workflows. These should tie into inventory movement, receiving, picking, or other inventory movement or usage-based workflows. Barcoding not only gives you verification of work and error prevention but in sophisticated systems, you can receive a log record of the action taken so you can dig back into it later if anything were to go wrong.
As an example, if someone miscounts the items they are putting away, this would give you the ability to see when the error happened and who made the error.
Picking Path Optimization
You can also design your warehouse in a way that increases efficiency when it’s time to pull stock for either order fulfillment or product distribution. These designs may differ greatly based on their intended use case.
Some common picking path methodologies are:
Serpentine Pick Path: picking up one face of racking or storage and coming back down from the opposite side, then starting up back the other side on the reverse side of the racking
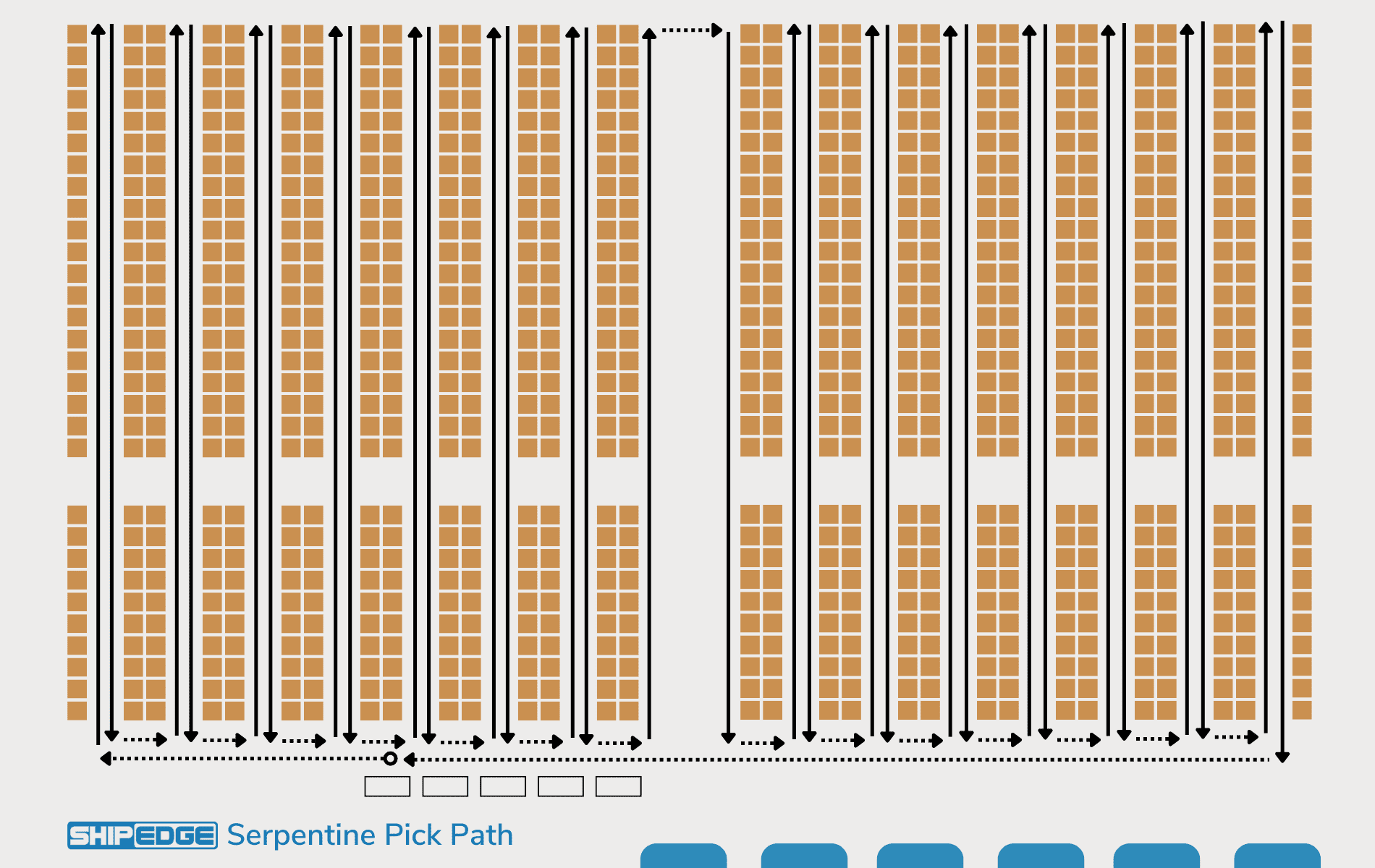
Zig-Zag Pick Path: Going up the same aisle of racking and picking from the left and right sides at the same time in a zig-zag or “z format” of movement.
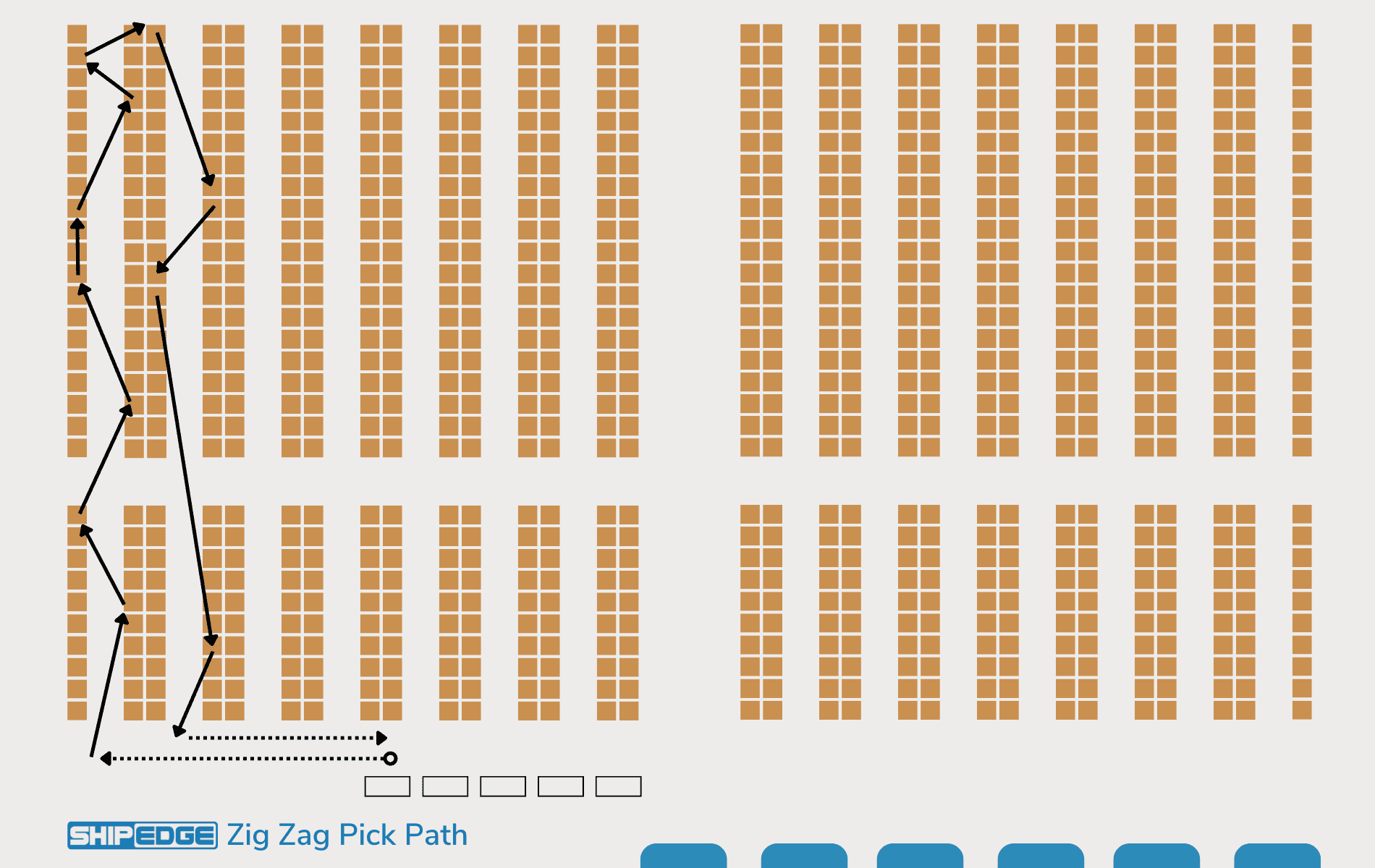
Zone-Based Pick Path: Picking orders or line items for an order from one zone at a time, prioritizing orders that can be completely picked from one zone if possible.
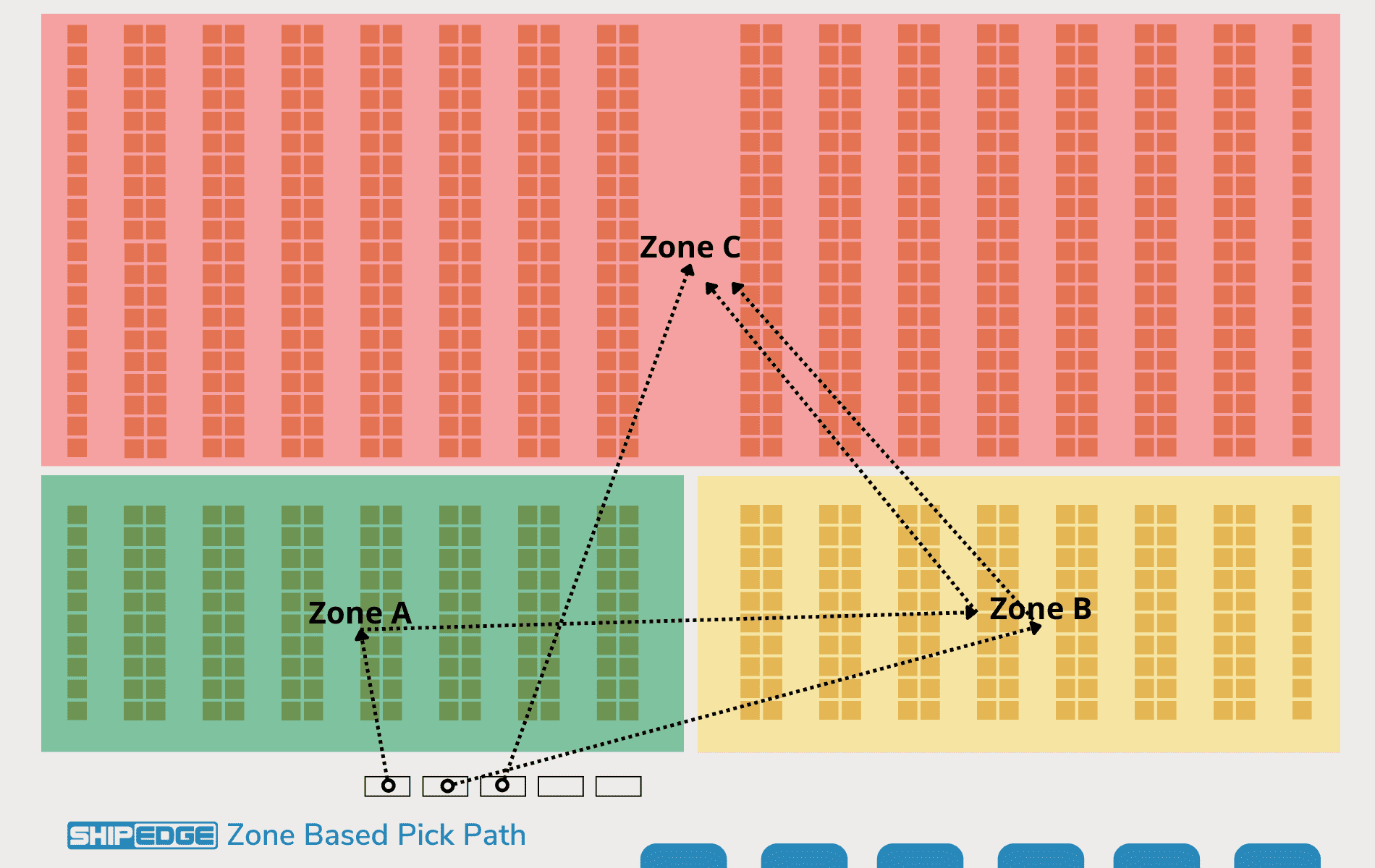
4. Integrated Shipping Desk/Best Rate Shipping Feature
Shipping is a critical aspect of any e-commerce business, especially when it comes to providing an amazing customer experience to drive repeat ordering and increase a customer’s lifetime value (LTV).
Being able to guarantee your customers that their products will be delivered on time to the right address is an important part of the eCommerce shopping experience.
Not everybody thinks, “hey! A WMS can help me with that,” when thinking about an efficient shipping process, because traditionally, WMS systems didn’t come with integrated shipping tools.
However, modern eCommerce Warehouse Management Systems that were intentionally built to tackle the challenges of online commerce, like Shipedge, have robust integrated shipping capabilities.
Simplifing Your Shipping Processes
When your WMS has robust shipping tools built-in, fulfillment workflows don’t break down at one of the most critical stages of order management in the warehouse.
From time to time, we still come in contact with new clients who are used to generating labels using a separate software from their WMS and were able to help them shift shipping operations into their primary system of work for the warehouse, the WMS.
This helps our clients ensure that the entire fulfillment process can be done within one system, which helps to:
- Reduce IT complexity by reducing the number of software a warehouse team member needs to use
- Make training easier and faster for new warehouse team members as fulfillment center teams experience turn over and a more competitive hiring market
- Prevent mistakes caused by manual data entry or recreating data from one system to another
- Simplify shipping by allowing for order and item scanning in workflows at any point in the shipping process
Reducing Costs with Rate Shipping
One of our most popular features is Best Rate Shipping. You are able to rate shop across 50+ carriers and their service levels, either with the click of a button or by creating automated rate shopping rules.
The automated option pulls accurate shipping rates in real time, even accounting for many common shipping surcharges, then selects the cheapest method that matches your settings related to max transit time or other considerations.
Integrated shipping in a warehouse management system that has rate shopping capabilities allows you to diversify your carrier and shipping service level strategy and decrease shipping spending.
Empowering Your Team with Automation
Order fulfillment automation can mean that parts of your shipping processes do not involve any user input at all. Most automation in a fulfillment or distribution center is designed to maximize the amount of work your warehouse team members are able to do in a given time span.
There are quite a few parts of the shipping process that can greatly benefit from some form of automation. Here are a few examples:
Carton Selection: Picking the right package type and size can be tedious and hard to train new members on. Cartonization tools in a WMS can help suggest the optimal packaging to your packers. This reduces workload and the cost of shipping over time by using the right size packaging.
Shipping Method Shopping: Rather than relying on rate charts or carrier by carrier rate shipping, we are able to take all of your relevant shipping carriers and service levels as they pertain to a specific order, pick the cheapest method that makes sense for the order programmatically, then generate the optimal shipping label.
Accompanying Document Printing: International shipments sometimes require paper trade documents. These are automatically generated and printed for the packing at the time of shipping. Other documents like attachments, special branded packing slips, or channel specific documents are also automatically printed according to settings or order data.
If you are in a 3PL/4PL business or work within a busy e-commerce warehouse, you know that ensuring cost-effective shipping is crucial in order to make profits and keep customers happy.
The Best Rate Shipping (BR) feature will have all your carriers integrated into your virtual shipping desk; this allows you to diversify your carrier usage strategy and decrease shipping spending.
Warehouse management systems will automatically rate shop between your carriers and ensure that you will be getting the best carrier in every fulfillment situation. Best rate shopping feature is a module that you will find in a truly end-to-end software solution.
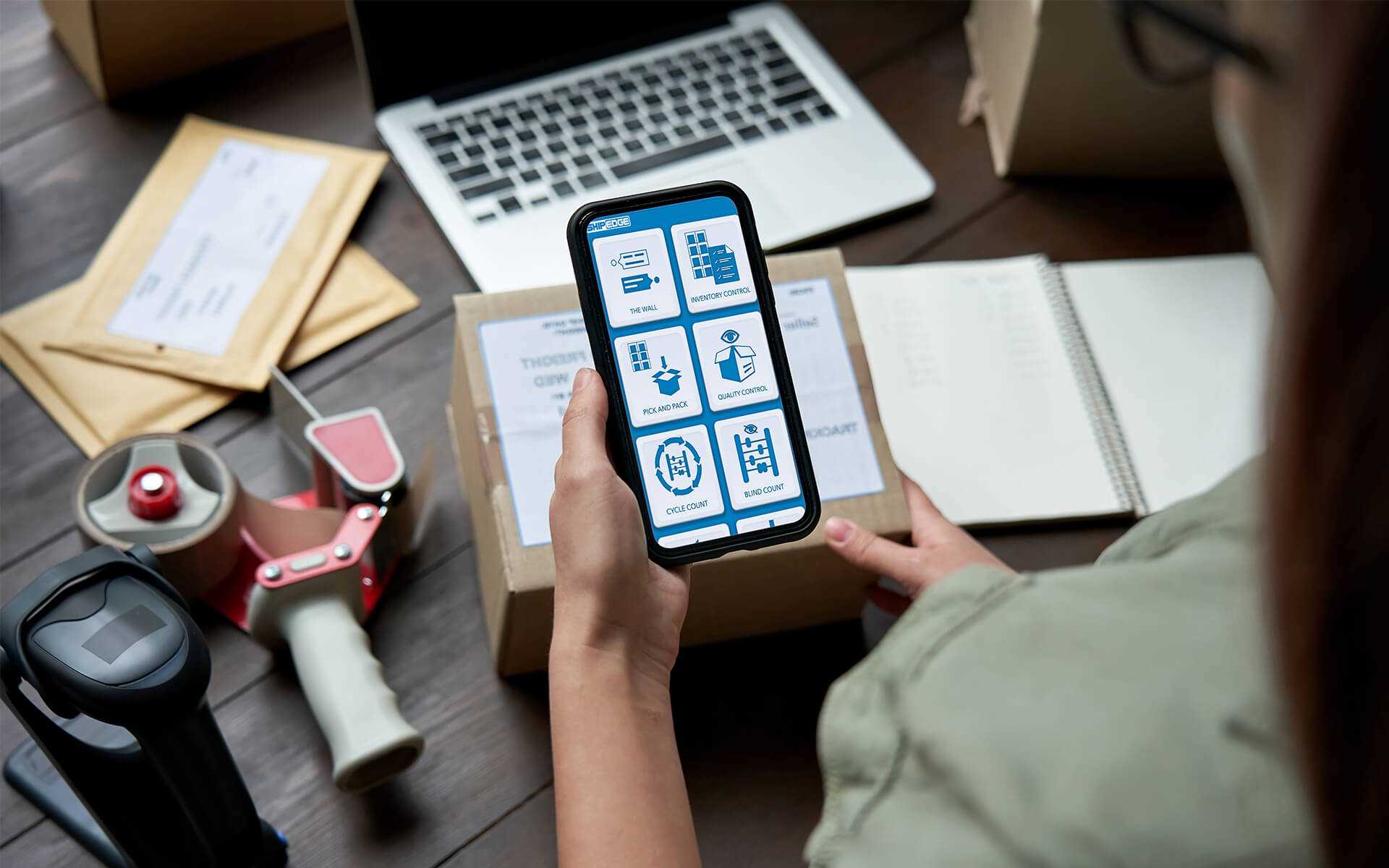
5. Ability to Grow Quickly and Sustainably
Managing orders, inventory, shipping, returns, and the teams that manage those warehousing and fulfillment processes can be challenging. By utilizing a warehouse management system, you will become more efficient in managing your entire fulfillment center from the minute your inventory arrives until that inventory is shipped.
Modernizing your operations allows you to spend more time increasing market share and growing your business, and less time micromanaging warehouse operations.
Building Scalable Processes
When creating logistics processes for your organization, keeping scalability in mind will allow you to meet the challenges of growth head-on as things inevitably change from day to day. Starting with something fairly rugged and simple is a good first step. Good warehouse management systems are built around workflows that keep industry best practices in mind. So selecting a good WMS ensures that you don’t have to define every workflow from scratch by yourself.
After you’ve defined your processes, you can use a warehouse management system to assist you in governance and making sure that your growing team adheres to the processes you put in place. Using software to create transparency and keeping people on the same page helps remove the need to do tedious micromanagement on a daily basis.
Removing Growth Limiters
Another common question fast-growing organizations should ask themselves is, “will this system be able to grow with me as my business growth drastically changes my operational needs?” Warehouse management software providers need to ask themselves, “can I support both a startup and a Fortune 500 corporation?” If the answer is yes, that means you’ve found a WMS that is a full lifecycle system. This means you can rest easy knowing that you’ve selected a system that will be a growth maximizer rather than a growth limiter.
We’ve been able to successfully deploy our warehouse management system on 5 of the 7 continents (6- if you consider that Antartica is uninhabited) and support customers ranging from fast-growing brands and logistics companies, to global household name brands. Our experience across different sizes of clients in many regions and verticals helps us to create software that is easy to deploy but has no problem scaling with your operations when it comes time to meet the challenges of explosive growth.
Meeting & Exceeding Customer Expectations
Whether you are a brand, wholesales, or third-party logistics company, you will have customers to answer to, and having a smooth logistics process will keep those customers happy and encourage repeat business.
A robust warehouse management system can help you create delightful e-commerce experiences after the initial purchase. Industry leaders like Amazon and Walmart have leveraged a software and robotics process to create these types of winning custom experiences by:
- Decreasing the cost of fast shipping and increasing on-time delivery
- Reporting accurate and real-time inventory to customer-facing eCommerce site
- Preventing errors when picking products for order fulfillment
Conclusion
The features highlighted in this post are by no means exhaustive, however, they are some helpful considerations to keep in mind if you are considering implementing an eCommerce-focused WMS.
When partnering with a software provider, consider whether or not they offer features that will allow you to grow your eCommerce logistics operations in a sustainable way.
To get started with Shipedge as your technology partner, book a free consultation with us here.