Pre-Manifest Picking is the process of preparing a shipment before you pick the items. In most cases, this means printing documents like packaging lists, shipping labels, and invoices. Alternatively, Post-Manifest picking is when you print these documents after you pick the order. Post-Manifest Picking is more common, but each method has its merits and downsides.
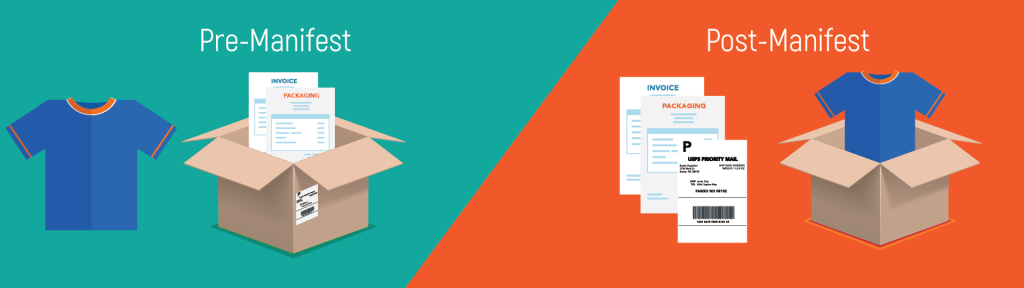
Examples:
You’ve received an order for one t-shirt.
Pre-Manifest Picking: You print a packaging list, shipping label, and invoice. Then you create a pick order. Then your picker picks the items. Once the items are picked, everything goes into/onto the box and the parcel is ready to ship.
Post-Manifest Picking: You create a pick order and your picker picks the T-Shirts. Then the picker takes the items to the packaging center. Your packer will print the documents and put the items into/onto the box and the parcel is ready to ship.
When to Use Pre-Manifest Picking
Generally speaking, pre-manifestation is faster, yet riskier. E-commerce companies like Amazon and eBay monitor how quickly you get an order out the door. The faster the better. The tracking number on your shipping label effectively says that you shipped an order before you picked it. That looks pretty good to Amazon. Moreover, you have the opportunity to charge a customer’s card before picking. If the card bounces, you save time and labor. When done well, pre-manifesting can cut your labor in half. Because labor is the most expensive variable cost, these savings can add up.
There are risks involved with Pre-Manifest Picking as well. For example, if your OMS is not up to par, you may pay for shipping only to find out that you don’t have the inventory to fulfill the order. All of the Klout you created with Amazon and eBay will backfire as they dock points for stock-outs. Also, you need dimensions and weight to accurately pre-manifest. Otherwise, you may pick an item only to find out that you need a different label. You’ll end up paying twice for a single shipment.
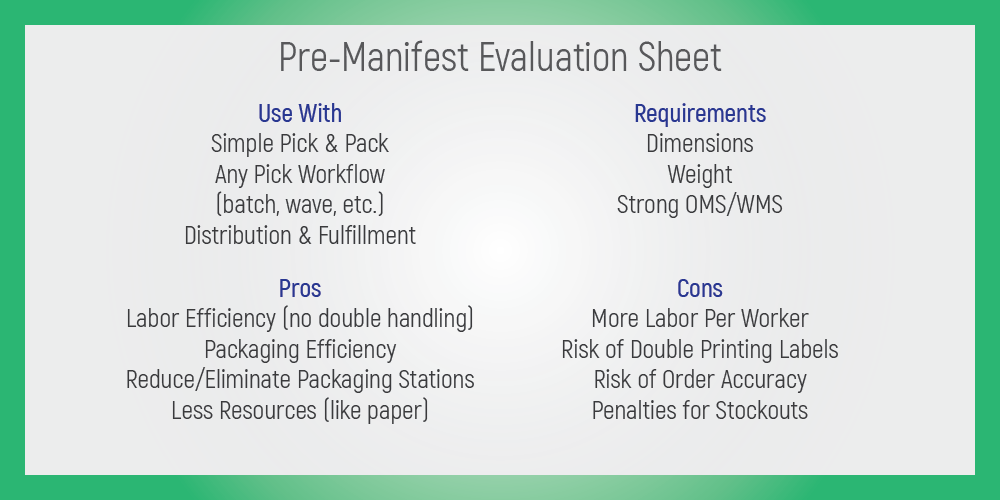
How Pre-Manifest Picking Works in Shipedge
When you first upload inventory in Shipedge you add dimensions. This includes physical dimensions as well as weight and any special information like serial or lot numbers. In addition, Shipedge tracks your inventory across every channel. Because Shipedge has all of the information, it’s very easy to pre-manifest.
Shipedge tells your picker what box or parcel you’ll need. If you want, you can pre-load the documents into the package and pick orders directly into boxes. The Shipedge app skips paper picking lists and lets your picker verify as they go. When everything is picked, you can seal the boxes or pass them off to a packer for Quality Control. Custom workflows let you manage the process and tweak it to your operation.
When to Use Post-Manifest Picking
Post-Manifest Picking is the traditional model. It will take a bit longer and you’ll need a dedicated packer. Many companies prefer post-manifest because managers have more visibility over the process. There are natural risks when you pass an order from one person to the next. Some organizations see this as an opportunity to catch mistakes.
If you are bundling, kitting, or manufacturing, it’s usually safer to use post-manifest. Bundles require more attention and time, so you may want to account for that. Some distribution centers prefer post-manifest because suppliers are not always accurate with dimensions. Also, if you ship internationally you can pre-manifest, but many organizations use post-manifestation to be cautious.
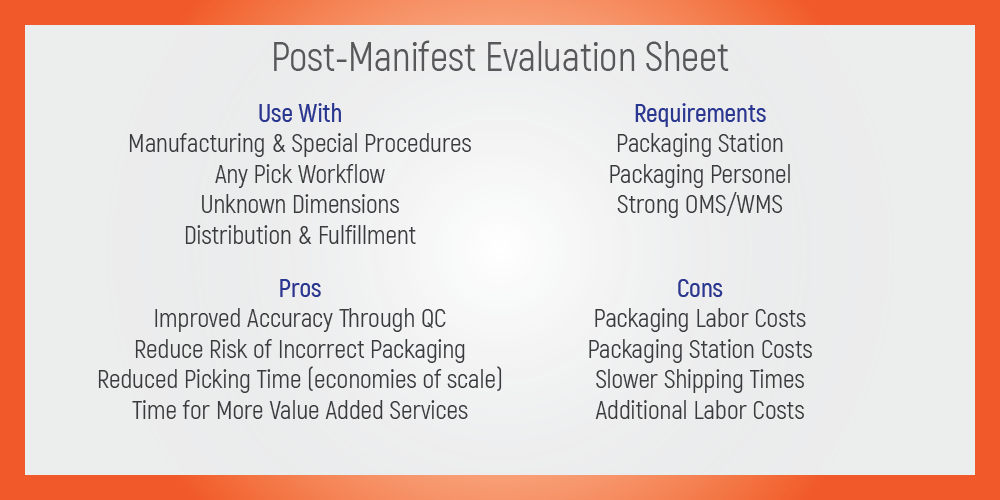
How Post-Manifest Picking Works in Shipedge
In Shipedge, Post-Manifest Picking works much the same as Pre-Manifest Picking. The only difference is the order in which you complete tasks. All of the information is still accurate, there is less paper involved, and pickers still verify as they go. Of course, the majority of operations do a mix of both, which Shipedge supports.
Conclusion
Pre-Manifest Picking and Post-Manifest Picking each have their place in fulfillment and distribution. It’s smart to play around with both to decide what fits your organizational needs best. In most cases, you will use a mix of both. You’ll have to test to find the right equilibrium. Remember that there are dangers to either, but only you know understand the true value of the risks and rewards.
Logistics is growing and changing at incredible rates. Consumers expect accurate orders at unprecedented speeds. Supply chain software is here to help you adapt to a developing market. Use the software. Test the workflows. Small adjustments today make a big difference at the end of the year.