Table of Contents
- What is Cycle Counting?
- Why do Warehouses Need Cycle Counting?
- When Should You Conduct Warehouse Cycle Counts?
- Using a Warehouse Management System to Cycle Count
- Conclusion
- FAQ: Click to Learn More
What is Cycle Counting?
Cycle counting is a selective inventory-counting method where a subset of inventory items or bins are counted on a specified day, rather than conducting a comprehensive inventory count all at once. By dividing the inventory into manageable portions and counting them regularly, businesses can achieve continuous stock visibility without interrupting daily operations.
The premise is simple: rather than shutting down annually for a wall-to-wall count, select portions of the inventory are counted regularly throughout the year. This ensures that over a defined period (typically a year), the entire inventory gets counted, if not multiple times.
What is a Blind Count?
Similar to a cycle count, blind counts are when laborers go into the warehouse and count the amount of inventory in specified bins, without knowing the total amount that is supposed to be there. The actions for each of these are identical, but conducting a blind count occurs with no knowledge about inventory levels.
Why do Warehouses Need Cycle Counting?
Cycle counting is more than just a counting procedure; it’s an essential inventory management strategy. Let’s dive deeper into the compelling reasons for its adoption.
Maintain Inventory Accuracy Without Disruption
One of the primary challenges warehouses face during full-scale physical counts is operational disruption. Closing down for a day or even a few hours can translate into significant revenue loss and delay in customer orders. With cycle counting, businesses can maintain a steady workflow. Regular, smaller counts prevent massive discrepancies from arising, making inventory records more accurate and trustworthy.
Proactive Problem Identification
By regularly checking on inventory, businesses can promptly spot issues, be it misplaced items, damaged goods, theft, or administrative errors. Early identification means early resolution, preventing minor problems from ballooning into significant crises. This proactive approach contrasts sharply with discovering a large discrepancy during an annual count, where the root cause might be an event from 11 months ago.
Cost-Efficiency
Mistakes in inventory can be costly. An incorrect stock level can lead to missed sales opportunities or over-purchasing. With cycle counting, the frequency of updates ensures that stock levels reflect reality, preventing unnecessary spending. It also reduces the man-hours needed for large-scale annual counts, which often require overtime or temporary staff hires.
Streamlining Operations and Reducing Waste
An accurate understanding of inventory aids in optimizing storage strategies, leading to better space utilization. Knowing what’s on hand and where it’s located reduces time wasted searching for items. This boosts picking efficiency and reduces the chances of items becoming obsolete or expiring on the shelves.
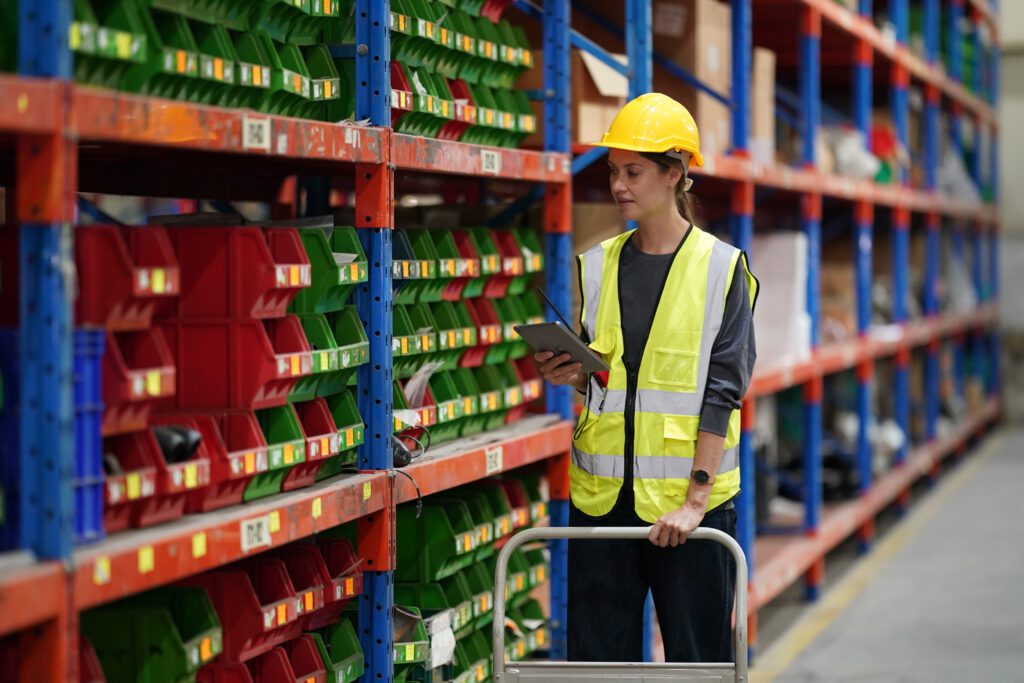
Boosted Employee Accountability and Training
Regular cycle counts naturally inculcate a sense of responsibility among warehouse staff. The knowledge that items will be frequently checked ensures a higher level of care during stock logging. Moreover, the regular process becomes a continuous training tool, helping employees become familiar with products, their locations, and the importance of accurate recording.
Enhanced Customer Trust and Satisfaction
Nothing erodes customer trust faster than an “Out of Stock” label, especially if they’ve already placed an order. With cycle counting ensuring inventory accuracy, businesses can confidently promise product availability to their customers. This accuracy translates into faster order fulfillment and fewer backorders or mistakes, leading to satisfied and loyal customers.
Data Integrity for Better Decision-Making
In today’s digital age, data is king. Accurate inventory data is invaluable for forecasting, trend spotting, and decision-making. Without consistent cycle counting, data may become outdated or misleading. Businesses can make more informed decisions about purchasing, sales strategies, and even marketing campaigns by ensuring data integrity.
Adherence to Regulatory Standards
For industries with stringent inventory-related regulations, cycle counting ensures that they remain compliant. This consistent checking and documentation can be a key element in regulatory adherence, especially where product traceability is essential.
When Should You Conduct Warehouse Cycle Counts?
The timing and frequency of cycle counting can vary based on a company’s needs, the nature of the products, and the size of the warehouse. Here are some common approaches to frequency:
- Daily Cycle Counting: Ideal for warehouses with a vast number of SKUs. A set number of items are counted daily to cover the entire inventory over a month or quarter.
- Weekly/Monthly/Quarterly Cycle Counting: Suitable for mid-sized warehouses. A larger portion of the inventory is counted weekly or monthly.
- ABC Cycle Counting: Inventory items are categorized based on their value and importance (A for high value or high volume, B for moderate, C for lower value or sell-through rates). ‘A’ items are counted more frequently than ‘B’ or ‘C’ items.
- Random Sample: As the name implies, this method involves selecting warehouse inventory at random to count.
Using a Warehouse Management System to Cycle Count
Warehouse Management Systems (WMS) will often have the ability to conduct cycle counts in the software itself. In Shipedge, both blind counts and cycle counts easily can be done in the mobile app.
After a cycle or blind count has been completed, a report is generated to notify the warehouse manager of any discrepancies found. The discrepancy can then be reported in the WMS to update inventory records.
Conclusion
The decision to implement cycle counting extends beyond the simple act of counting stock. It’s a strategic move that touches on multiple facets of warehousing, from cost-saving to customer satisfaction. As businesses seek ways to streamline operations and enhance efficiency, cycle counting stands out as a tried-and-true method with manifold benefits.